Blacksmithing and Wrought Ironwork
Research is important before buying any product and wrought iron railings, gates, artwork and restoration work is no exception.
Researching Blacksmithing and Wrought Ironwork
To help you make an informed decision before commissioning any wrought ironwork we have provided answers to some of the questions we are asked and questions you should ask.
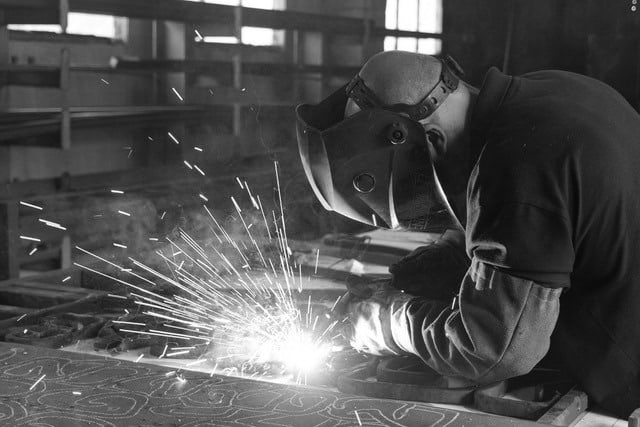